In the quick-moving universe of mineral mining, where productivity and security are vital, transports assume a significant part in smoothing out material taking care of cycles. Mining transports are mechanical frameworks intended to move mass materials, like metal, starting with one area and then onto the next inside the mining activity. This far-reaching page digs into the fundamental parts of transports in the mineral mining industry, featuring their importance, applications, key parts, and advantages.
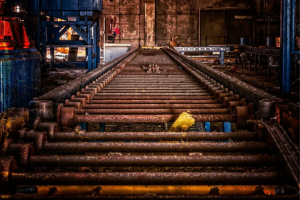
Belt Transports
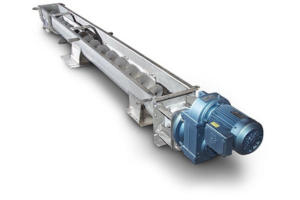
Auger and screw conveyors
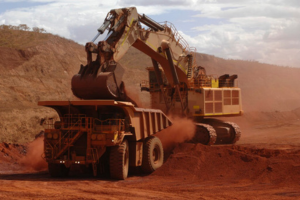
Can Lifts
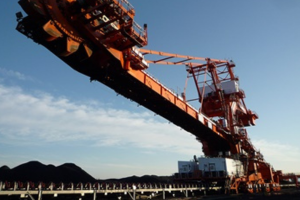
Stackers and Reclaimers
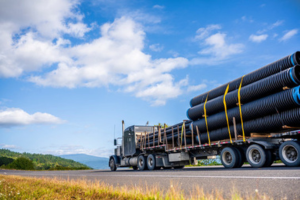
Pipe Transporters
A type of belt conveyor that is enclosed in a housing shaped like a pipe is called a pipe conveyor. They are utilized to ship materials, including metals and minerals, over significant distances and in Earth’s delicate regions. The encased plan forestalls spillage and residue discharges, making them ideal for applications where ecological insurance is vital.
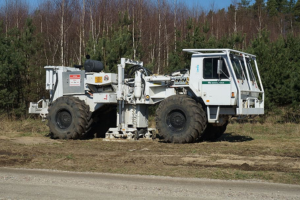
Vibrating Transports

Link Belt Transports
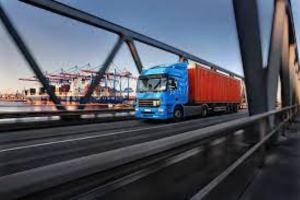
Portable Transports
Advantages of Using Conveyors in Ore Mining
- Further developed Productivity: Transports work with a nonstop progression of materials, limiting personal time and enhancing general mining processes.
- Cost Decrease: By decreasing the requirement for manual taking care of and haulage, transports lower work and upkeep costs, prompting expanded benefits.
- Upgraded Security: Transports take out the dangers related to manual material taking care and large equipment activity, advancing a more secure workplace.
- Natural Obligation: Through the use of conveyors, efficient material transportation and waste disposal contribute to environmentally responsible mining practices.
All in all, transports have reformed material taking care of in the mineral mining industry, driving proficiency, security, and efficiency. They are now a necessary asset for modern mining operations due to their extensive applications, essential components, and numerous advantages. By embracing transport innovation, mineral mining organizations can remain ahead in a cutthroat market, boost efficiency, and maintain natural stewardship for feasible development and achievement.
The Most Important Parts of Mining Conveyors
- Further developed Productivity: Transports work with a nonstop progression of materials, limiting personal time and enhancing general mining processes.
- Cost Decrease: By decreasing the requirement for manual taking care of and haulage, transports lower work and upkeep costs, prompting expanded benefits.
- Upgraded Security: Transports take out the dangers related to manual material taking care and large equipment activity, advancing a more secure workplace.
- Natural Obligation: Through the use of conveyors, efficient material transportation and waste disposal contribute to environmentally responsible mining practices.
All in all, transports have reformed material taking care of in the mineral mining industry, driving proficiency, security, and efficiency. They are now a necessary asset for modern mining operations due to their extensive applications, essential components, and numerous advantages. By embracing transport innovation, mineral mining organizations can remain ahead in a cutthroat market, boost efficiency, and maintain natural stewardship for feasible development and achievement.
The Most Important Parts of Mining Conveyors
- Belt Conveyor: The transport line, made of tough materials, conveys and transports the mass materials or minerals. It very well may be customized to the particular necessities of the mining activity, guaranteeing effective and solid material exchange.
- Rollers and Idlers: Support structures along the transport line, intended to diminish grating and backing the belt’s weight, guaranteeing smooth and persistent activity.
- Pulleys: Used to redirect the belt or give pressure, keeping the belt rigid and forestalling slippage.
- Drive System: An electric motor, gearbox, and other components make up the heart of the conveyor system, which gives the conveyor the power and control it needs.
- Unit for Take-Up: adjusts the tension of the conveyor belt in response to changes in temperature and wear.
Utilizations of Transports in Metal Mining
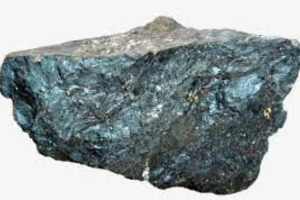
Extraction of Ore
Material Vehicle
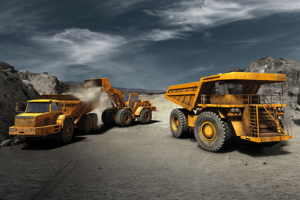
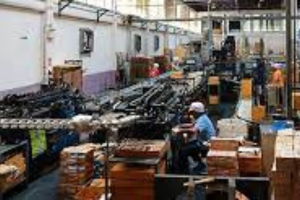
Handling Plants
Stockpiling
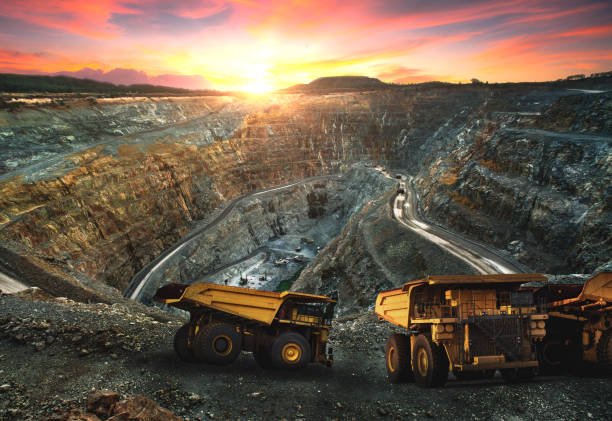
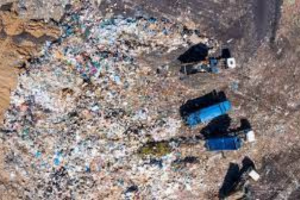