Cross-docking is a planned operations process where approaching merchandise is straightforwardly moved from inbound vehicles to outbound vehicles with negligible or no in the middle between. Conveyors assume a crucial part in cross-docking operations, giving a dependable and proficient answer for flawlessly moving merchandise among vehicles and improving the progression of materials inside the distribution center. This page investigates the crucial job of conveyors in cross-docking operations, the different kinds utilized in distribution centers, their applications, as well as the advantages and difficulties related to their execution.
Kinds of Conveyors Utilized in Cross-Docking Operations in the Distribution Center

Belt Conveyors
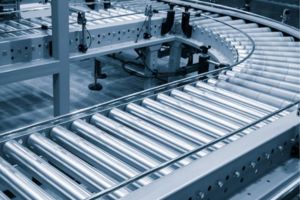
Roller Conveyors
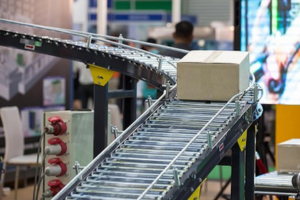
Gravity Conveyors

Adaptable Conveyors
Advantages of Conveyors in Cross-Docking Operations in the Stockroom
- Proficiency: Conveyors in cross-docking operations fundamentally lessen material dealing with time, empowering quicker throughput and request handling.
- Streamlined Space Use: Cross-docking with conveyors limits the requirement for broad warehousing, taking into account proficient utilization of accessible space.
- Diminished Stock Holding Expenses: Cross-docking decreases stock holding costs as merchandise are quickly moved, lessening capacity time and related costs.
- Upgraded Production Network Dexterity: Conveyors add to a more lithe production network, empowering ideal and responsive request satisfaction.
The Job of Conveyors in Cross-Docking Operations in the Distribution center
Conveyors act as a critical part of cross-docking operations in distribution centers, offering fundamental capabilities:
- Fast Material Exchange: Conveyors empower quick and smooth exchange of approaching products from inbound trucks or compartments to outbound vehicles, limiting dealing with time and capacity necessities.
- Arranging and Steering: Conveyors coordinated with sortation frameworks successfully sort and course items given the objective, guaranteeing precise and proficient stacking onto the suitable outbound vehicles.
- Improved Stacking and Dumping: Conveyors smooth out the stacking and dumping processes, taking into consideration the concurrent treatment of various things, diminishing bottlenecks, and expanding throughput.
- Limited Stock Holding: Cross-docking with conveyors lessens the requirement for broad warehousing and extra room, empowering a more spry and practical store network.
Uses of Conveyors in Cross-Docking Operations in the Distribution Center
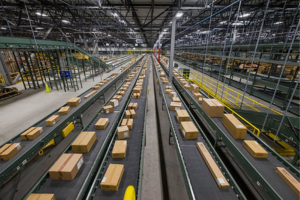
Direct Exchanges
Sortation and Directing
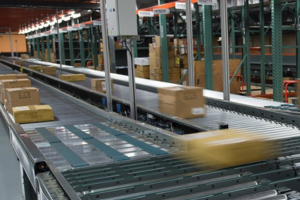
