Loading and unloading merchandise in a distribution center can be a work serious and tedious cycle. Notwithstanding, with the joining of conveyors, this critical part of stockroom tasks turns out to be fundamentally more productive and smoothed out. Conveyors assume an imperative part in mechanizing the development of merchandise among vehicles and distribution center offices, offering various advantages and tending to different difficulties. How about we dig into the role of conveyors, the various kinds utilized in stockroom loading and unloading, their applications, as well as the benefits and difficulties related to their execution?
Sorts of Conveyors Utilized in Loading and Unloading in Stockroom
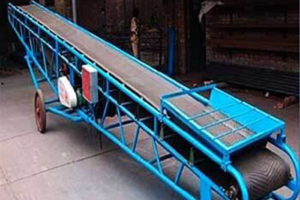
Belt Conveyors
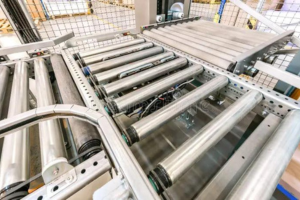
Roller Conveyors

Adaptive Conveyors
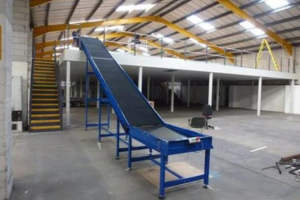
Adaptable Conveyors
Advantages of Conveyors in Loading and Unloading
- Time Investment funds: Conveyors speed up loading and unloading processes, decreasing completion times for vehicles and expanding general efficiency.
- Decreased Work Expenses: Via robotizing manual errands, conveyors limit the requirement for physical work, prompting cost reserve funds and streamlined asset allotment.
- Space Improvement: Conveyors amplify stockroom space usage by productively moving merchandise between the loading moor, capacity regions, and outbound transportation zones.
- Further developed Well-being: Conveyors upgrade working environment security by limiting manual handling and diminishing the gamble of wounds during loading and unloading activities.
The Role of Conveyors in Loading and Unloading
Conveyors are a critical part of distribution center loading and unloading, empowering a smooth exchange of merchandise between trucks, trailers, compartments, and the stockroom premises. Their fundamental role can be summed up as follows:
- Proficient Exchange: Conveyors work with the productive exchange of merchandise among vehicles and the distribution center, lessening the requirement for manual handling and accelerating the loading and unloading process.
- Limited Margin time: Via computerizing the development of merchandise, conveyors guarantee a ceaseless progression of items, limiting personal time and improving by and large functional productivity.
Space Improvement: Conveyors are intended to upgrade space usage in stockrooms, productively moving merchandise from the loading moor to capacity regions or straightforwardly to outbound delivery regions. - Flexible Applications: Conveyors are versatile and can be incorporated into different loading and unloading situations, obliging various kinds of items and burden sizes.
Uses of Conveyors in Loading and Unloading in Stockroom
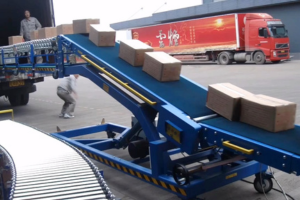
Truck Loading and Unloading
Holder Loading and Unloading
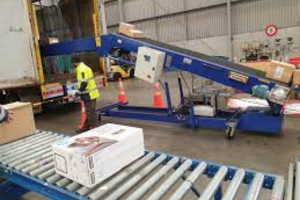
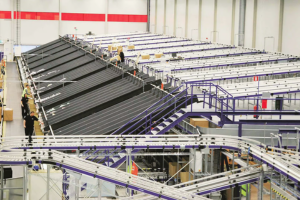
Cross-Docking Offices
Dissemination Focuses
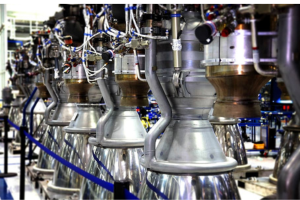